Build for Living. Report.
P14 of 31
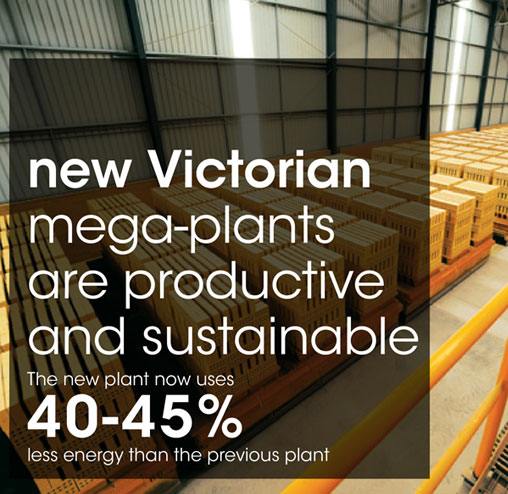
new victorian mega-plants are productive and sustainable
The 600 hectare site on Melbourne’s northern fringe has been the site of brick manufacture since the late 1940’s, largely thanks to its extensive deposits of clay and shale. It now holds two identical brick plants that have ultimately replaced three redundant plants and demonstrated remarkable savings in energy and raw materials, increased productivity and product quality and improved air quality.
Brickworks Building Products™ $125 million investment in these plants demonstrates its faith in the future of the industry and its commitment to replacing redundant plant with state-of-the-art facilities.
Onsite clay and shale extraction
Most of the constituent minerals of bricks and pavers are extracted on site, reducing transport costs. The site has reserves of approximately 50 years for the most popular clay types, increasing to 200 years for some lower usage minerals.
Lower energy consumption
Scale, automation, efficient design, 24/7 operation and the extensive use of variable-speed electric drives in place of hydraulic or pneumatic drives combine to lower electricity consumption to one-third less than that of a comparable conventional plant. Natural gas consumption has been slashed: The kilns use onethird less gas than comparable conventional kilns. The dryer tunnels use only kiln exhaust heat.