Build for Living. Report.
P10 of 31
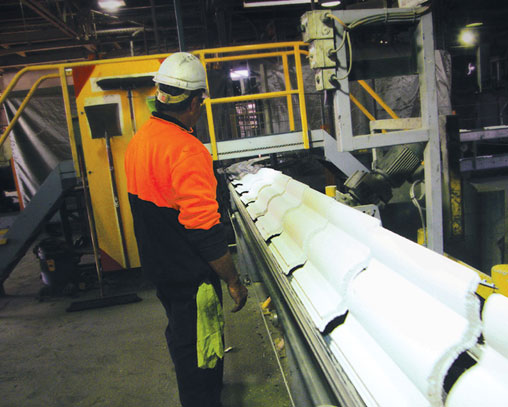
improving manufacturing inputs
Australia has abundant supplies of natural gas which led to the conversion across the group of brick, block and tile kilns from oil many decades ago. As well as being cost effective, natural gas generates considerably lower greenhouse gas emissions than the generation of electricity of the same energy value.
Reducing energy consumption continues to be a key target especially in high consumption operations such as brick manufacture. The high-capacity, state-of-the-art kilns at Austral Bricks® Wollert (Victoria) plants use a remarkable one-third less gas than a comparable conventional brick kiln.
However, even older kilns are capable of improvement as demonstrated by the installation of new high-efficiency burners in the firing zone at Austral Bricks® Horsley Park Plant 21 which resulted in a 15 percent productivity improvement and similar energy savings.
Improvements have also been made in kiln door sealing at Bristile Roofing™ concrete roof tile plants. Although these kilns operate at a much lower temperature than a brick kiln, there are still substantial savings to be made.
Considerable savings have also been made by process improvements such as the conversion from high maintenance, high energy consumption pneumatic and hydraulic drives and constant-speed electric drives to variable-speed electric drives.
Thanks to these and other initiatives, Brickworks Building Products™ has slashed its greenhouse gas emissions by over 30 percent since 2000.